3 min read
Why Forged Components Outperform Cast in Fracking Operations
Southwest Steel Processing
:
April 7, 2025
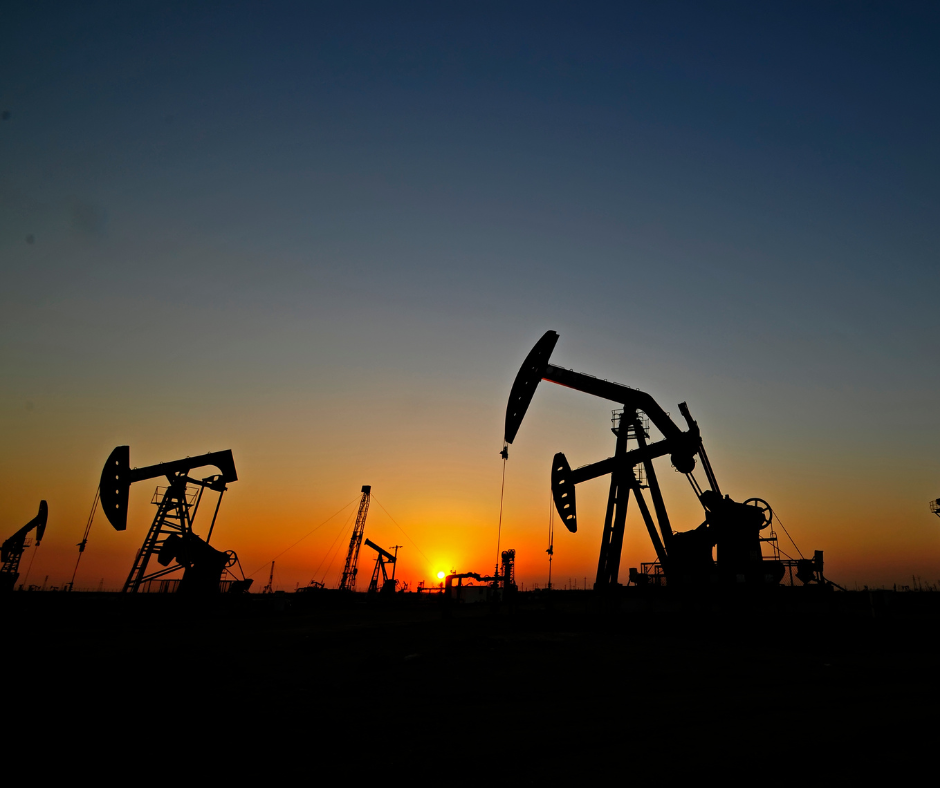
Reducing Downtime. Increasing Reliability. Elevating Performance.
In the high-stakes world of oil and gas, every component in your frac spread plays a critical role in operational efficiency and safety. From frac pumps to wellhead assemblies, parts are routinely exposed to intense pressure, high flow rates, abrasive fluids, and aggressive chemical environments. Failure in these conditions isn’t just inconvenient—it’s expensive, hazardous, and potentially catastrophic.
That’s why leading OEMs and equipment manufacturers across the energy sector are turning to Southwest Steel Processing (SSP). With a reputation for producing high-performance forged components that withstand the extreme demands of hydraulic fracturing, SSP offers a proven solution to a recurring industry challenge: component failure. Whether you're managing power end housings, valve blocks, or crossovers, the difference between a forged part and a cast one can mean the difference between costly downtime and uninterrupted productivity.
At SSP, we understand that your equipment needs to work harder, last longer, and perform reliably under the harshest operating conditions. Our American-made forged steel components are designed with the goal in mind—to help you minimize downtime, control replacement costs, and keep your operations running smoothly. When reliability is critical, forging isn’t just a better option—it’s the right one.
Forged vs. Cast: What’s at Stake in Fracking Environments?
While casting may offer lower upfront costs and faster prototyping, it often comes at the expense of structural integrity and lifecycle performance. In high-pressure hydraulic fracturing environments, cast components are more vulnerable to cracking, porosity, and fatigue. This leads to frequent replacements, increased maintenance, and unexpected downtime.
Forging, on the other hand, delivers superior strength and consistency. The process aligns the grain flow of the steel with the shape of the part, enhancing fatigue resistance and mechanical performance—exactly what’s needed when operating pressures soar and equipment cycles are nonstop.
For more information on forging vs casting download our whitepaper.
Key Advantages of Forged Components in Fracking Applications
When it comes to high-pressure fracking operations, the materials you choose can either be your greatest asset—or your biggest liability. Forged components offer distinct advantages over cast alternatives, especially in environments where failure is not an option. At SSP, we focus on delivering forgings that are built for the extremes—where strength, reliability, and service life aren’t just features, but requirements.
From superior mechanical properties to a more resilient supply chain, here’s why forged parts from SSP consistently outperform cast components in the field:
- Superior Strength and Impact Resistance
SSP’s forged parts handle higher loads without cracking under pressure. Whether it’s for power end housings, valve bodies, or fluid end components, forged steel outperforms cast every time. - Longer Component Life, Lower Replacement Rates
Frequent replacements add up. Our forged solutions are engineered for endurance, significantly reducing the need for costly service interruptions and part swaps in the field. - Tighter Grain Structure, Fewer Failures
Forged steel is denser and free from the internal voids or porosity found in castings. That structural integrity minimizes failure risk in safety-critical applications. - Made in the USA and Delivered on Time
In an industry where delays are measured in lost revenue, you need a dependable supplier. SSP offers domestic production and a streamlined supply chain, ensuring reliable delivery—even when global markets get turbulent.
These advantages aren’t theoretical—they’re proven in the field, across some of the most demanding oil and gas applications. Whether you’re designing new equipment or looking to improve the reliability of an existing product line, SSP’s forged solutions provide a measurable performance edge. Let’s talk about how we can strengthen your supply chain and your bottom line with parts that are built to last.
Facing the Real Challenges in the Field
In the oil and gas industry, equipment is expected to perform without compromise—often under the most extreme conditions. Unfortunately, that’s not always the case. Component failures, rising maintenance costs, and supply chain delays have become common pain points for operators and OEMs alike, disrupting schedules and cutting into margins.
At SSP, we take a different approach. Our forged components are engineered to deliver the strength and reliability needed to keep your operations running without interruption.
Struggling with part failures in the field? Cast components often fall short in high-pressure environments, leading to fatigue and failure when it matters most. SSP’s forged steel components are built for endurance, offering superior fatigue strength that helps prevent mid-operation breakdowns.
Tired of constant replacements driving up costs? We understand that frequent part turnover doesn’t just impact your budget—it affects productivity and performance. Our long-lasting forged parts are designed to reduce downtime and lower your total cost of ownership over time.
Concerned about unreliable lead times? With ongoing disruptions across global supply chains, having a dependable, domestic supplier matters more than ever. SSP’s U.S.-based operations ensure consistent quality and timely delivery, so you’re never left waiting for critical components.
When the pressure is on, equipment failure isn’t just an inconvenience—it’s a risk. SSP is here to help you mitigate that risk with durable, high-performance forging solutions built for the demands of modern fracking operations.
Built for Pressure. Backed by Experience.
At SSP, we understand that in the oil and gas industry, there’s no room for compromise. Equipment must perform flawlessly under relentless pressure, abrasive materials, and extreme operating conditions. That’s why our forging solutions are built from the ground up to deliver unmatched strength, reliability, and consistency—job after job.
With decades of expertise and a fully automated domestic forging operation, SSP delivers high-performance components that meet and exceed the demands of modern fracking environments. Our commitment to precision engineering, rigorous quality standards, and responsive customer support makes us a trusted partner to OEMs and equipment manufacturers across the energy sector.
When uptime, safety, and longevity are on the line, forged components aren’t just a better choice—they’re a strategic advantage. At SSP, we don’t just meet expectations. We forge ahead of them.