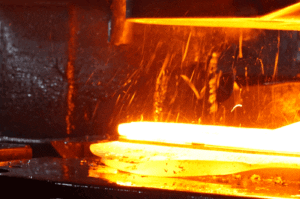
Forging vs. Casting
Forging and casting are two popular methods used to manufacture products. While both methods have their own advantages and disadvantages, there are several benefits of forged products over casted products. Here are some points to consider:
- Strength: Forged products are stronger than cast products due to the process of shaping metal under high pressure, which improves its grain flow structure and makes it denser. This makes forged products more durable and long-lasting than casted parts.
- Material properties: Forged products have better material properties compared to casted products. The forging process aligns the grain structure of the metal, which enhances its mechanical properties, such as toughness, ductility, and fatigue strength.
The Science Behind The Forging Process
Forging processes employ mechanical force to shape metal billets, such as rolling, pressing, hammering, or similar techniques, while they remain solid. This heating and deformation process refines the internal grain structure of the metal by allowing metallurgical recrystallization to occur. This results in a more uniform structure throughout the metal form, giving it greater strength and resistance to impact and shear damage.
The benefits of forging processes are numerous, making it a popular choice for shaping metal billets.
Forged metal parts are known for their high strength and durability, making them ideal for use in high-stress applications. The uniform grain structure that results from the forging process also makes the metal more resistant to fatigue and cracking, which can be critical in applications where failure is not an option.
Because the metal is shaped while it is still solid, forging can create parts with a high degree of accuracy and detail, which can be important in critical industries such as aerospace or medical device manufacturing.
There are a variety of forging techniques available, each with its own strengths and limitations. For example, rolling can be used to create long thin parts while hammering is better suited to creating complex shapes and profiles.
Finally, it's worth noting that forging processes can be more energy-efficient than other metal-shaping techniques, such as casting. Overall, the combination of energy efficiency, strength, and flexibility makes forging a highly attractive option for manufacturers who are looking to reduce their environmental impact while still producing high-quality parts.
It's also important to note that while forging produces stronger and more durable parts, it may not be suitable for creating highly complex shapes or intricate designs. In these cases, casting may be the better option.
Casting: An Effective Method for Producing Complex Parts
The process of metal casting involves pouring molten metal directly into an existing mold. The cast metal then cools and hardens into a solid state the exact shape of the mold. Manufacturers choose from various types of molds based on order size and part complexity.
Although metal casting has been used for centuries, it is now primarily used for parts that are too large or unwieldy for metal forging. Casting is an ideal method for creating intricate geometries that cannot be produced through the application of force alone.
Benefits of metal casting over forgings in certain scenarios, when it comes to creating metal parts, casting can be an excellent alternative to forgings, particularly because of the following benefits:
- Fewer Restrictions on Size and Complexity: Castings can be created for parts of virtually any size or complexity level, making it a versatile option.
- Greater Range of Metal Options: A wider range of specialty alloys can be used in castings since chrome, nickel, and molybdenum can be more easily incorporated into the molten metals.
- Cost-Effective for Low-Volume Production: Castings are ideal for producing small production runs more cost-effectively, particularly since the tooling is cheaper than the equivalent forging dies.
Ultimately, the decision between forging and casting comes down to a variety of factors, including the specific requirements of the project, the available budget, and the desired end result.
By carefully considering all of these factors, you can choose the best production method for your project and ensure high-quality, reliable results.
Overall, while casting may be a more cost-effective option for certain products, forging offers unique benefits in terms of strength and material properties that cannot be obtained in any other way. Forged parts are superior and are preferred in critical application areas where the parts must perform at the highest level.
For more information on our forging capabilities contact us.