4 min read
Forgings vs. Castings: Superior Attributes with SSP
Southwest Steel Processing
:
May 14, 2024
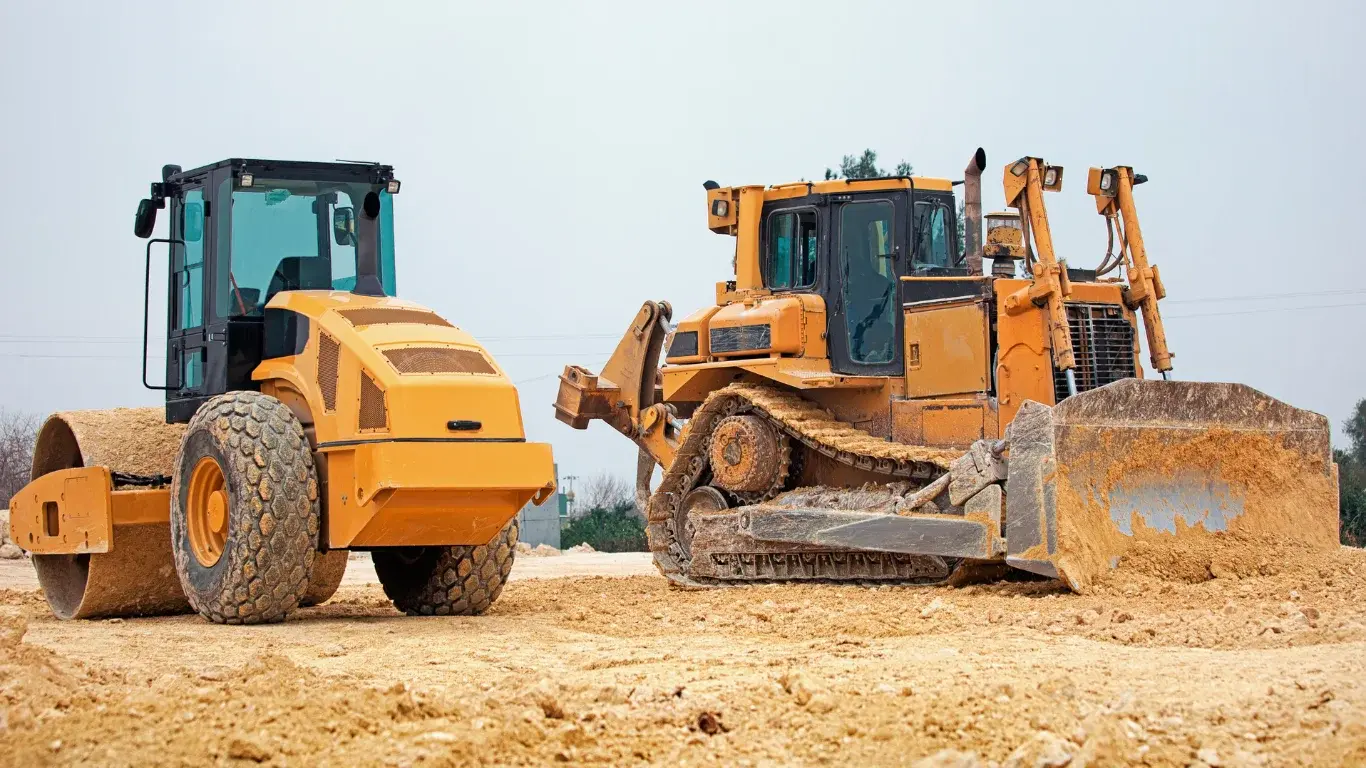
Introduction
In the realm of manufacturing, the debate between using forgings and castings is pivotal, particularly when it involves components that demand high durability and strength. Southwest Steel Processing (SSP) specializes in producing superior forged components that offer enhanced performance over casted alternatives.
This decision impacts a broad spectrum of industries, including automotive, aerospace, construction, and mining, where the durability of components could be the requirement for operational success. The choice between forgings and castings does not solely hinge on the technical benefits and limitations of each process. Economic factors and the application's demand level play crucial roles as well.
For many projects, particularly those with lower performance requirements or stringent budget constraints, castings can provide a cost-effective solution without significantly compromising quality. However, in scenarios that demand high durability and are subject to extreme operational stress—such as in industries such as Aerospace, Construction & Mining, Oil & Gas, Rail, and critical automotive systems—forgings are unequivocally superior.
In this article, we will delve deeper into the distinctions between forgings and castings, examining their respective advantages and limitations across various applications. By understanding these differences, industries can make more informed decisions about which manufacturing process best suits their specific needs for durability, cost-efficiency, and performance under stress. We will provide detailed insights and real-world examples, including a case study from Southwest Steel Processing, to illustrate why forgings often provide the best solution for high-demand applications.
What are Forgings and Castings?
Forgings involve shaping metal using localized compressive forces, which are applied through various techniques such as hammering, pressing, or rolling. This process does not melt the metal; instead, it changes its physical shape by applying extreme pressure in a solid state, often after heating the metal to increase its plasticity. The key to forging's superiority lies in the continuity of the metal grain structure which aligns with the component's final shape, thereby enhancing its mechanical properties significantly.
Castings, however, are created by pouring molten metal into a mold to achieve the desired shape. Once the metal cools and solidifies, it retains the shape of the mold but lacks the uniform structural integrity seen in forged parts. This method is preferable for complex shapes and sizes but often introduces imperfections such as porosity (tiny holes formed by gases), shrinkage (reduction in size as the metal cools), and inclusions (trapped impurities) which can weaken the metal.
Why Forging Often Outperforms Casting
Forging's predominant advantage over casting is its unparalleled strength and reliability. The intense compression during the forging process refines the metal's grain structure, making it denser and aligning it in one direction which significantly enhances its tensile strength and fatigue resistance. This grain flow strengthens the part throughout, particularly crucial in applications involving high pressures and temperatures.
In high-intensity applications such as mining teeth, where components are required to withstand extreme pressures and impacts, forging unequivocally outperforms castings. The superior mechanical properties of forged mining teeth, including their enhanced durability and resistance to wear and tear, make them indispensable in mining operations where equipment reliability is paramount. By opting for forgings, industries benefit from reduced downtime, lower maintenance costs, and extended equipment life, affirming that in scenarios demanding the utmost strength and resilience, forging is the definitive manufacturing choice.
Case Study: Optimizing Mining Tooth Performance
SSP's capabilities in forgings are vividly illustrated through their success in optimizing the performance of mining teeth used in excavators. Mining teeth, crucial for efficient excavation and durability, traditionally used castings which wore out quickly under harsh mining conditions.
A Canadian Oil Sands Mining Company faced frequent replacements of their excavator's mining teeth, which led to increased downtime and operational costs. By switching to SSP's forged mining teeth, they observed a 40% increase in lifespan and significantly reduced the frequency of replacements, optimizing operational efficiency and cost-effectiveness. Read more here.
Attribute | Forgings | Castings |
---|---|---|
Attribute |
Higher, due to aligned grain structures |
Lower, due to potential for internal voids |
Toughness |
Improved toughness and fatigue resistance |
Less tough, with greater brittleness |
Production Costs |
Higher initial costs but less waste |
Lower initial costs, higher defect rate |
Customization |
High flexibility in customization |
High flexibility in customization |
Precision |
Higher precision and consistency |
Can vary due to shrinkage upon cooling |
Why Forging Often Outperforms Casting in High-Demand Applications
Optimized Grain Flow: Forgings are formed through a process of deforming the metal, allowing the internal grain of the material to flow and align with the component's shape. This alignment significantly enhances the part's strength and fatigue resistance, particularly important in high-impact and high-stress applications.
Inherent Strength and Durability: The forging process compacts the metal, resulting in a denser and more robust component. Forged parts exhibit superior tensile strength and maintain their structural integrity even under extreme conditions.
Thermal Resistance and Reliability: Forged components are less likely to succumb to thermal fatigue and maintain their performance characteristics at higher temperatures compared to castings. This makes them ideal for use in engines and other high-temperature environments.
When Castings Outweigh Forgings
Despite the advantages of forgings, castings have their place in industrial applications where complexity and cost are more critical than the ultimate strength and performance. Cast parts:
Are more cost-effective for creating complex shapes due to the versatility of the mold process.
Require less machining and finishing work, which can significantly reduce production costs for parts with intricate designs.
Provide sufficient strength and durability for applications where operational conditions are less severe.
Environmental and Economic Considerations
Forged parts often represent a higher initial investment than cast parts. However, the longevity and durability of forgings translate into lower overall lifecycle costs due to less frequent replacements and maintenance needs. For industries like mining where equipment must endure abrasive environments, the robustness of forgings leads to significantly enhanced productivity and reduced downtime.
From an environmental and economic perspective, forgings are increasingly proving more beneficial. Forgings are typically stronger than castings, allowing for the use of less material to achieve the same level of performance which leads to lighter, more efficient designs.
Furthermore, the enhanced durability of forged parts means less frequent replacements and repairs, translating into lower lifecycle costs and reduced material waste. Although the initial costs for forged parts might be higher than those for cast parts, the total cost of ownership over time, including maintenance and operational costs, is often much lower with forgings.
SSP's Forging Excellence
Southwest Steel Processing is renowned for its advanced forging techniques and high-quality outputs. SSP’s forging process involves sophisticated equipment and skilled craftsmanship to produce parts that reliably perform under the most strenuous conditions.
SSP employs state-of-the-art technology to ensure each forged part meets stringent quality standards. Their products go through rigorous testing to verify their strength and durability, ensuring they exceed customer expectations.
Next Steps
Are you looking to enhance the durability and performance of your equipment? Consider the superior quality of forged parts from Southwest Steel Processing. With proven expertise and a commitment to excellence, SSP delivers not just parts, but peace of mind.
Visit Southwest Steel Processing to explore our solutions and find out how our forging capabilities can enhance your operational efficiency.
Get in Touch
At SSP, we're not just offering a service – we're providing a partnership that drives innovation and efficiency in forging. By encompassing all critical steps of the forging process and offering the unique No-Cost Stocking Program, we ensure top-tier quality, efficiency, and customer satisfaction. Join us in setting new standards in the forging industry.