3 min read
Built to Withstand the Load: Why Forged Components Are Essential in Large-Scale Construction Projects
Southwest Steel Processing
:
July 10, 2025
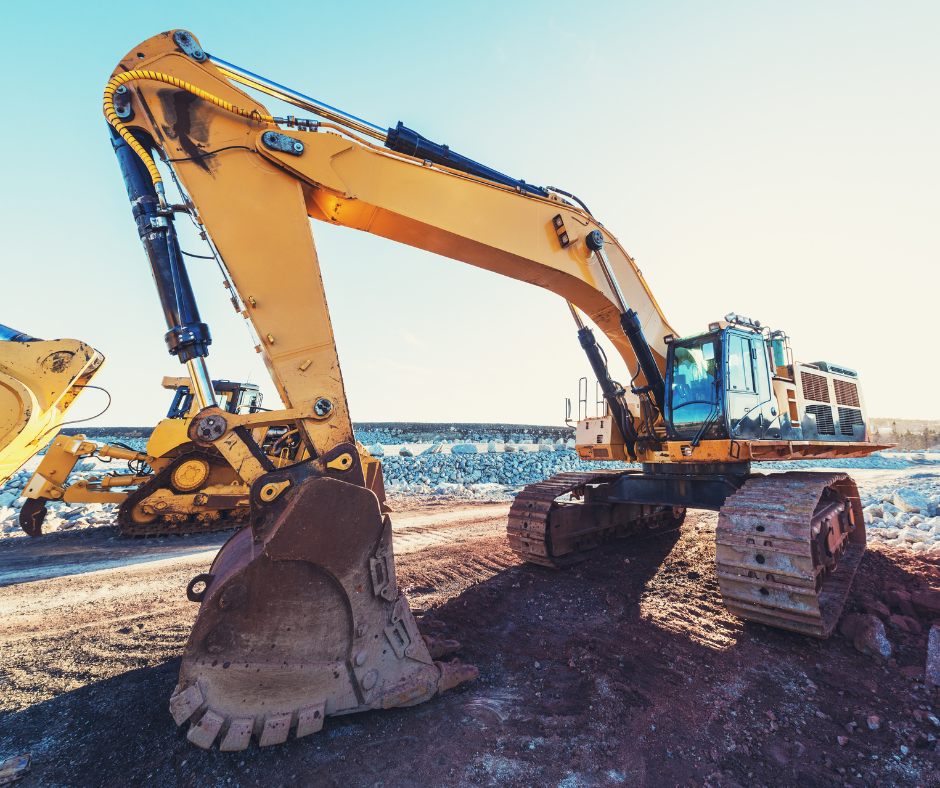
As America’s infrastructure faces renewal and expansion, the machines behind the build—excavators, haulers, bulldozers, cranes, and heavy-duty trucks—must perform without fail. At the core of their performance lies something deceptively simple yet absolutely critical: forged components.
These parts carry the weight of the work, often unseen, but essential to uptime, safety, and cost control. At Southwest Steel Processing (SSP), we specialize in providing high-strength forged components that serve as the foundation for durable, high-performance equipment. From track links to transmission components, we forge the future of construction—one part at a time.
Why Forging Is the Backbone of Construction Equipment
Construction environments are unforgiving. Machines are exposed to dirt, dust, shock, and massive loads, often for 12- to 16-hour shifts. This level of abuse makes casting and machining less-than-ideal options for critical components. That's where forging stands apart.
Forging refines the metal’s grain structure and compresses voids, producing parts that are:
- Stronger and more impact-resistant
- Less susceptible to cracking, fatigue, and wear
- More consistent across production batches
According to industry leaders and forging experts, forged components consistently outperform other manufacturing methods in construction applications because they’re engineered to endure extreme conditions—not just perform under them.
Typical forged parts in construction applications include:
- Bucket teeth, track links, and undercarriage systems
- Structural support pins, arms, and yokes
- Drive train components, transmission shafts, and flanges
- Cylinder bodies and coupling elements
When equipment fails on-site, the downtime is measured in thousands of dollars per hour. Forged components help minimize that risk.
The SSP Difference: U.S.-Based Forging with End-to-End Solutions
At SSP, we do more than produce parts—we engineer custom forging solutions tailored to your specifications, performance standards, and delivery timelines. From construction equipment OEMs to tier-one suppliers, our team supports your production goals with consistency and scale.
Our Arkansas-based facility features:
- 6,000- and 7,000-ton forging press lines, producing up to 2,000 parts per day per line
- In-house machining, heat treatment, and induction hardening
- Quality testing, full part traceability, and ISO 9001:2015 certification for performance assurance
- U.S.-based production for supply chain stability and shorter lead times
We don’t outsource. We deliver domestic reliability, responsive customer service, and cost-competitive production that supports your bottom line.
Real-World Results:
When a customer in the off-highway equipment industry needed a cost-competitive, high-volume forging solution to meet their annual production needs, SSP delivered. We produced a complex, near-net shape component with minimal material waste—providing a long-term, scalable solution that continues to support the customer’s equipment performance today.
Serving Three Industries with One Forging Solution
One of SSP’s strategic strengths is our ability to serve construction, tractor/agriculture, and heavy-duty truck industries with the same level of engineering excellence and material integrity.
That overlap means OEMs can:
- Standardize component sourcing across equipment lines
- Ensure uniformity in quality and certifications
- Streamline supply chain partnerships with a single, dependable provider
From the track systems of an earthmover to the drivetrain of a heavy-duty truck hauling materials across the country, SSP’s forged components carry the weight of the job—literally and figuratively.
Why Top OEMs Trust SSP for Forged Construction Equipment Parts
Top manufacturers choose SSP not just for quality, but for the peace of mind that comes with:
- Durability Under Pressure – Parts designed to endure the most punishing field conditions
- Scalability – We meet volume demands without sacrificing quality
- Agility – Short lead times and fast turnarounds from our U.S. facility
- Engineering Support – Collaborate on part development, PPAPs, and machining specs
- Customer Commitment – Our team works with yours to solve problems and deliver outcomes
These aren’t just parts—they’re high-performance, precision-engineered solutions.
Forging vs Casting: What Construction Equipment Needs
The construction market is often tempted by the lower up-front cost of cast parts—particularly for non-load-bearing applications. But as equipment grows in size, complexity, and function, casting’s limitations become costly liabilities.
Feature |
Forging |
Casting |
Grain Flow |
Controlled and aligned |
Random, often includes voids or porosity |
Fatigue Resistance |
High |
Low |
Impact Strength |
Excellent |
Moderate |
Dimensional Control |
Precise |
Less consistent |
Durability |
Long-lasting |
More prone to failure |
For OEMs focused on long-term performance, safety, and cost-efficiency, forging is the clear winner—especially in high-stress, high-impact applications like those found in construction, trucking, and heavy equipment.
Want a deeper comparison of forging vs. casting?
Download our detailed whitepaper:
👉 Forging vs. Casting: What Construction Equipment Really Needs
Infrastructure Investment Means More Forging Demand
Since the passage of the Bipartisan Infrastructure Law in 2021, billions in federal funding have continued to fuel large-scale infrastructure projects across the U.S.—and 2025 is no exception. With construction activity still surging, the demand for reliable, high-performance equipment remains at an all-time high.
That means:
- Increased equipment demand to support ongoing public works, transportation, and energy infrastructure
- Accelerated fleet replacements to keep up with project timelines and evolving safety standards
- Heightened emphasis on part reliability as OEMs aim to minimize downtime and maximize ROI
Southwest Steel Processing stands ready to support that demand. With high-volume forging capacity, U.S.-based production, and decades of experience in critical industries, SSP is the trusted partner for OEMs, equipment builders, and tier-one suppliers navigating the next phase of America’s infrastructure expansion.
Let’s Build It Strong—Let’s Build It Together
If you manufacture or support construction, trucking, or tractor equipment, SSP can deliver the custom-forged solutions you need to lead your market.
Track links. Bucket teeth. Suspension parts. Engine supports. If it needs to hold, haul, pull, lift, or dig—we’ve forged it.
Let’s connect and show you how SSP can help you reduce downtime, improve part life, and deliver confidence in every component.