CASE STORY: High-Volume Cost Competitive Forgings
- Home
- Case Stories
- High-Volume Cost Competitive Forgings
Large Railcar manufacturer realizes the value of sourcing their Center Plates locally.
Case Study: High-Volume cost competitive forgings needed to meet high volume annual needs.
Customer: The largest Rail Car truck assembly supplier in North America.
Industry: Rail
Application: 70,000+ Low Profile Center Plates needed annually to meet all North America’s Railcar manufacturing needs.
Problem:
The customer required high volumes of forged center plates—these parts are extremely difficult to obtain from a North American supplier, who can offer a globally competitive price. The typical overseas lead time ranges from a minimum of 20 weeks. In addition to the extended overseas lead time the political climate internationally puts overseas supply chains at high risk.
The long lead times and the supply chain uncertainty from their current supplier proposed the issues of material shortage which impacted their manufacturing capabilities.
Solution:
Southwest Steel Processing (SSP) is fully automated and can forge up to 1,500 center plates per day on its 7,000-ton press forging line. This allows SSP to provide the quantities needed to support the entire rail industry at a globally competitive price, with shorter lead times for the domestic customers.
SSP Advantage:
SSP’s steel supplier is integrated with the manufacturing process, therefore the lead times for steel is short, and their capacity for manufacturing is shortened with available raw materials. This enables SSP to compete with global competitive pricing – as they maintain the lowest cost industry steel pricing with no transportation costs.
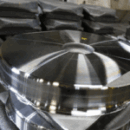
Forging Advantages
Railroad, mining, industrial machinery, and gear customers choose forgings over castings in critical application areas because they know quality can’t be compromised. Critical applications demand forging because it delivers:
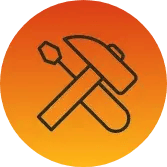
Stronger end products due to a tighter grain structure
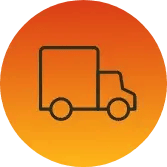
Products that are true to form with little porosity or cavities
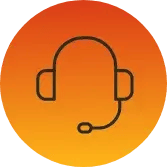
Fewer weak points because forging reduces the need to fabricate multiple components
Quality Assurance
Our quality management systems meet international standards, which means we consistently provide products and services that fulfill customer and regulatory requirements.

ISO 9001:2015 Certified
.webp?width=39&height=39&name=icon_1%20(1).webp)
AAR M-1003 Certified
American Association Railroads
.webp?width=39&height=39&name=icon_1%20(2).webp)
ISO 14000
Compliant
.webp?width=39&height=39&name=icon_1%20(3).webp)
Mitutoyo
FHM4CMM
.webp?width=39&height=39&name=icon_1%20(4).webp)
Magnetic Particle
testing certified
.webp?width=39&height=39&name=icon_1%20(5).webp)
Level three
PPAP capable