CASE STORY: FORGED RAILCAR DRAFT LUGS
- Home
- Case Stories
- Forged Railcar Draft Lugs
Minimizing lead times with unique, no cost, ship from inventory stocking program.
Customer: One of the largest railcar manufacturers in North America.
Industry: Rail
Application: 100,000+ draft lugs needed annually
Problem:
The customer required high volumes of forged draft lugs—these draft lugs are extremely difficult to obtain from a North American supplier. The typical overseas lead time ranges from a minimum of 20 weeks. The long lead times from their current supplier proposed the issues of material shortage which impacted their manufacturing capabilities and the ability to accept more orders limiting their revenue growth potential.
Solution:
Southwest Steel Processing (SSP) is fully automated and can forge up to 3,000 parts per day on their two forging lines. Enabling SSP to produce the large quantiles the customer required, in a shorter time compared to international supplier. SSP’s forging runs are based on “die life’s” which means they forge roughly 5,000 of each part in a single run.
SSP Advantage:
SSP’s advantage is their ability to run fast high-volume forging runs. This allows parts to get processed and transition into inventory. SSP can forge quarterly, semi-annual, or annual production amounts, they then keep the customer’s parts in their inventory at no additional cost. This stocking ability allows the customer to decrease the excess of on hand parts, allowing them to order as need.
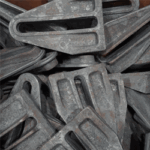
Forging Advantages
Railroad, mining, industrial machinery, and gear customers choose forgings over castings in critical application areas because they know quality can’t be compromised. Critical applications demand forging because it delivers:
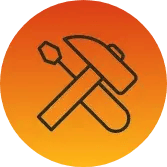
Stronger end products due to a tighter grain structure
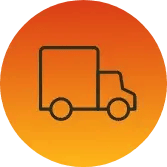
Products that are true to form with little porosity or cavities
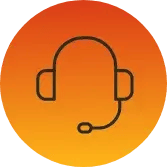
Fewer weak points because forging reduces the need to fabricate multiple components
Quality Assurance
Our quality management systems meet international standards, which means we consistently provide products and services that fulfill customer and regulatory requirements.

ISO 9001:2015 Certified
.webp?width=39&height=39&name=icon_1%20(1).webp)
AAR M-1003 Certified
American Association Railroads
.webp?width=39&height=39&name=icon_1%20(2).webp)
ISO 14000
Compliant
.webp?width=39&height=39&name=icon_1%20(3).webp)
Mitutoyo
FHM4CMM
.webp?width=39&height=39&name=icon_1%20(4).webp)
Magnetic Particle
testing certified
.webp?width=39&height=39&name=icon_1%20(5).webp)
Level three
PPAP capable