3 min read
The Key to Reliable and Productive Construction Equipment
Southwest Steel Processing
:
May 26, 2023
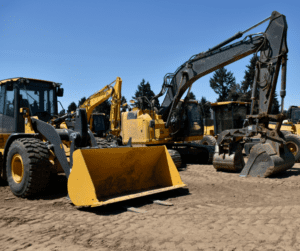
The construction industry demands heavy-duty equipment that can withstand the rigors of harsh environments and heavy workloads. At Southwest Steel Processing (SSP), we manufacture forgings that are critical components of construction equipment such as mining teeth and track links.
In this article, we will discuss the importance of forgings in construction equipment and why choosing forged components over casted components is the superior choice. We will also highlight the importance of American-made and reshoring efforts for OEMs of construction equipment. Lastly, we will share a case study that showcases the benefits of SSP's single-source solution for machined track links.
The Importance of Forgings in Construction Equipment
Forgings offer superior strength, durability, and reliability compared to castings. These qualities make forgings the ideal choice for construction equipment components that are subjected to heavy loads, shock, and wear.
The process of creating forgings involves heating and shaping metal under high pressure, which results in a finished product that is much denser and material strength stronger than castings or other components made through different manufacturing processes.
This high-pressure forging process allows the metal to take on a specific shape and size, while also producing a uniform grain structure throughout the metal, meeting the customer demands. This uniformity results in a final product that is less prone to cracking or breaking under stress, making it the ideal choice for critical components in construction equipment, such as mining teeth, track links, and other vital components.
The strength and durability of forgings ensure that these components can withstand the harsh conditions and heavy use they are subjected to on construction sites, ultimately increasing the safety, reliability, and productivity of the equipment.
Unlike forgings, castings are created by pouring molten metal into a mold and allowing it to cool and harden, resulting in a less-dense material that is more prone to defects and failures. Because of the casting process, the resulting material often has a less uniform grain structure and may contain voids or other imperfections that can weaken the material and make it more susceptible to stress cracking, corrosion, and other forms of wear and tear.
In addition, the cooling process during casting can cause residual stresses in the material that can cause it to warp or deform over time. As a result, castings may be more likely to fail prematurely or require frequent maintenance and replacement, which can lead to increased costs and downtime on construction sites and propose safety concerns for construction workers operating the equipment. Compared to castings, forgings offer a superior level of strength and durability, making them the preferred choice for critical components in construction equipment.
The importance of high-quality components in construction equipment cannot be overstated. By withstanding harsh conditions and heavy loads, forged components offer a longer service life and lower total cost of ownership than castings. According to industry research from the Forging Industry Association (FIA), forgings can last up to 20 times longer than castings, making them a smart investment for OEMs of construction equipment.
The Benefits of American-Made and Reshoring Efforts
Choosing American-made components for construction equipment can provide many benefits, including higher quality, faster lead times, and stronger supply chain relationships. Reshoring efforts can also help to reduce reliance on offshore suppliers and ensure that critical components are readily available when needed.
While many companies have turned to overseas suppliers to reduce costs and increase profit margins. Intended as a cost-effective solution, it can also lead to a variety of negative impacts on the supply chain. Longer lead times, increased shipping costs, and quality issues can all arise from working with overseas suppliers.
In addition, the COVID-19 pandemic has highlighted the importance of having a reliable domestic supply chain. According to a survey by Thomasnet.com, 83% of North American manufacturers are now considering reshoring their operations to ensure greater supply chain resilience and increase their pandemic preparedness.
By choosing United States manufactured components, construction companies can reduce their reliance on offshore suppliers and ensure that they have access to high-quality forgings when they need them. SSP's commitment to American-made forgings and reshoring efforts means that our customers can trust us to provide reliable and high-quality components, manufactured from American raw materials, for their construction equipment.
Case Study - Single-source Solution for Machined Track Links
SSP's single-source solution for machined track links, case study, provides a prime example of the benefits of forgings for construction equipment components. In this case study, SSP worked with an OEM of construction equipment to provide machined track links that were manufactured using our superior forging processes.
As a result, the OEM was able to reduce lead times, increase productivity, and ensure the reliability of their equipment. This case study demonstrates the benefits of working with a trusted partner like SSP for all of your construction equipment component needs.
Read our case study: Single-source Solution for Machined Track Links
Conclusion
Choosing forgings over castings is the superior choice for construction equipment components. Forgings offer superior strength, durability, and reliability compared to castings, which can pose significant risks to equipment and workers. By choosing American-made forgings and working with a trusted partner like SSP, OEMs of construction equipment can ensure that their equipment is reliable and productive.
Don't forget to check out SSP's industry pages and read our case study on single-source solutions for machined track links to learn more.