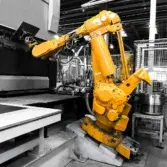
Automation has revolutionized the forging industry by increasing Quality, and efficiency and reducing labor costs. Automated robots use computer-controlled technology to produce high-quality metal forgings with precision and consistency.
This has led to improved safety, reduced waste, increased energy efficiency, and increased production capacity. The use of automation also allows for greater customization and flexibility in the manufacturing process. Overall, automation has played a significant role in the modernization of the forging industry.
Southwest Steel Processing is one of the few fully automated, high-volume custom forge shops in North America. We specialize in manufacturing quality forging components, all while maintaining fast lead times. Our dedication to automation and efficiency allows us to offer customers top-notch, high-quality, forged components quickly and reliably.
Even though forging is one of the oldest metalworking methods, it still proves to be highly efficient in today's day and age.
The History
Forging is the procedure of shaping metal without letting it fully melt. The metal stays solid while an operator uses metal forming techniques like hammering, rolling, or pressing. Forging has many variations, often involving heating the metal to high temperatures to make shaping easier.
Dating back to at least 4000 BC, and likely even earlier, early humans practiced the art of forging metals like bronze and iron to create hand tools and weapons for warfare. Forging during this time period was completed by hand.
During the 19th century, forge smiths were skilled at hand and open die process of wrought iron and became adept at hammer welding to create large shaft forgings.
The Bessemer steel-making process, invented in 1856, revolutionized the industry by providing a low-cost supply of steel for production. The first cavity steel using a closed die process began in the United States in 1862 for the Colt revolver components.
The industrial revolution caused significant changes to the industry, as new and improved tools and methods were developed. Initially, hammers were powered by a line shaft, but the invention of more compact electrical motors enabled each hammer to be operated separately, resulting in increased productivity and better organization of the production area.
World War II had a positive impact on the development of better equipment as the industry was absolutely essential to the war effort.
The invention of solid-state electrical induction heaters in the latter half of the 20th century resulted in increased productivity through better dimensional control and higher throughput in the processes.
The Industry Today
Today, the industry relies heavily on the use of automation in the metal forming process. Automated processes can enhance a company's productivity, decrease expenses, and enhance the quality of its products. The use of automated forging allows for precise temperature and pressure control, resulting in reliable and consistent parts.
The modern forging industry has achieved higher levels of control and forging efficiency with computer-controlled automation, as well as updated designs of induction heaters that utilize modern computing power. This has enabled the industry to produce a wide range of components in various materials for use in the railcar, mining, construction, and energy sectors.
Automating forging operations can significantly increase productivity, with potential increases from several hundred pieces per hour to up to 3,000 depending on the product type.
Value-added features like quick die changes should also be considered an aspect of forging automation, allowing the manufacturer to minimize nonproductive time and produce quality parts economically.
Automation in the industry has also helped to improve safety by reducing the number of manual tasks performed by workers, minimizing human error, and enhancing the precision and consistency of the manufacturing process. This has led to a decrease in accidents and injuries in the workplace.
The SSP Advantage
SSP manufacturing lines are fitted with robotic material handling automation to achieve consistent and repeatable quality, capable of producing forgings ranging from 30 to 300 pounds. Ajax/CECO/Erie Press, our sister company, is the leading supplier of forging equipment in North America. They provide us with top-quality forging presses and exceptional service and support.
Our automated forging process has been shown to enhance tensile strength, fatigue strength, versatility, and uniformity, providing numerous benefits like high volume production.
- According to a University of Toledo study, forged parts have 26% higher tensile strength compared to cast-iron components, enabling them to withstand more tension without tearing.
- When subjected to heavy-duty operating conditions, forged components exhibit greater fatigue strength and a longer lifespan compared to components made by other methods.
- Forging techniques offer great versatility in manufacturing a wide range of products, both big and small. Opting for casting instead of forging just to achieve a desired shape is seldom necessary.
- Forged components have a more consistent uniform composition and structure compared to cast ones, resulting in a longer lifespan.
- Automated processes enable the manufacturing of a large quantity of forged components.
Automation solutions in the forming processes have revolutionized manufacturing by providing repeatability, reliability, and efficiency. Our process is highly automated, ensuring that every step is executed with precision and consistency, resulting in high-quality products. From start to finish, our automated system enhances our ability to produce parts quickly and effectively.
For more information on our automated process contact our trusted sales team today.