CASE STORY: Single-source Solution for Machined Track Links
- Home
- Case Stories
- Single-source Solution for Machined Track Links
Construction and Mining OEM utilizes SSP as a single Source for Bulldozer Track Links.
Case Study: Single-source solution for machined forged parts.
Customer: The largest Construction / Mining equipment manufacturer in North America.
Industry: Construction / Mining
Application: Track links for D8, D9, D10 and D11 Bulldozers.
Problem:
The customer required high volumes of forged and machined track links. The customer has the capability to machine their forgings, however with the labor market struggles their capacity at their facilities was limited. It is not common for forgers to machine parts—therefor customers of forgers must secure and qualify a machining source. Because the customer had this step in the manufacturing process lead times and cost increased.
Solution:
Southwest Steel Processing (SSP) is fully automated and can forge up to 3,000 parts per day on their two forging lines. Enabling SSP to produce the large quantities the customer required, in a shorter time compared to international supplier. SSP also has the capabilities and capacity to do the machining needed on these forgings.
SSP Advantage:
SSP’s machining capabilities saves the customer time, money, and hassle of additional suppliers. SSP has the ability to rough or finish machining the customer’s forgings, eliminating the need for the customer to qualify an additional source, there is no need for purchasing to place another set of orders for the same parts. Lead times and transportation costs are cut down dramatically with a single source forger.
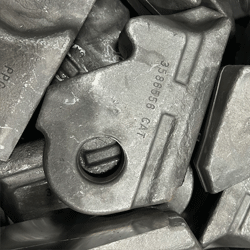
Forging Advantages
Railroad, mining, industrial machinery, and gear customers choose forgings over castings in critical application areas because they know quality can’t be compromised. Critical applications demand forging because it delivers:
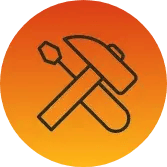
Stronger end products due to a tighter grain structure
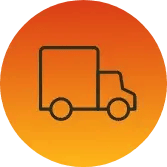
Products that are true to form with little porosity or cavities
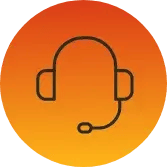
Fewer weak points because forging reduces the need to fabricate multiple components
Quality Assurance
Our quality management systems meet international standards, which means we consistently provide products and services that fulfill customer and regulatory requirements.

ISO 9001:2015 Certified
.webp?width=39&height=39&name=icon_1%20(1).webp)
AAR M-1003 Certified
American Association Railroads
.webp?width=39&height=39&name=icon_1%20(2).webp)
ISO 14000
Compliant
.webp?width=39&height=39&name=icon_1%20(3).webp)
Mitutoyo
FHM4CMM
.webp?width=39&height=39&name=icon_1%20(4).webp)
Magnetic Particle
testing certified
.webp?width=39&height=39&name=icon_1%20(5).webp)
Level three
PPAP capable