CASE STUDY: Optimizing Mining Tooth Performance for Enhanced Excavator Durability
- Home
- Case Stories
- Optimizing Mining Tooth Performance for Enhanced Excavator Durability
The Advantages of Forged Mining Teeth over Castings
Case Study: Optimizing Mining Tooth Performance for Enhanced Excavator Durability: The Advantages of Forged Mining Teeth over Castings
Customer: Canadian Oil Sands Mining Company
Industry: Mining
Application: Mining teeth for Excavators.
Problem:
The customer, operating in the mining industry, faced a significant challenge in maintaining the desired lifespan of their excavator’s mining teeth. The strenuous tasks performed by these machines subjected the mining teeth to excessive force, resulting in premature breakage. The sand was also wearing the teeth out much faster than what the normal life expectancy is. This raised concerns about the cost and operational efficiency associated with the frequent replacement of mining teeth. Their investigations were performed to determine the primary causes of accelerated mining tooth wear and breakage, considering factors such as material quality, design limitations, and maintenance practices. The customer was solely utilizing mining teeth that were casted.
Solution:
To address the customer’s concern regarding the short lifespan of their excavator’s mining teeth, SSP successfully provided a viable solution by offering high-quality forged Mining Teeth. Through rigorous testing and evaluation, the customer determined that forged mining teeth outperformed castings, offering an impressive increase of over 40% in lifespan specifically tailored to their mining application.
SSP’s expertise in the field of forging allowed them to deliver mining teeth of exceptional quality and durability. The customer benefited from the inherent strength and reliability of forged materials, which proved to be superior in withstanding the demanding conditions of their mining operations.
Extensive testing was conducted to validate the performance of the forged mining teeth, ensuring that they met the customer’s rigorous standards. The results obtained demonstrated a significant improvement in the lifespan of the mining teeth compared to castings previously used by the customer.
The implementation of high-quality forged mining teeth not only extended the lifespan but also provided the customer with several advantages. These benefits included enhanced productivity, reduced downtime associated with frequent replacements, and optimized operational efficiency.
By selecting SSP’s forged mining teeth, the customer effectively mitigated the issue of accelerated wear and breakage, which had been a significant concern. The durability and reliability of these forged components ensured prolonged service life and reduced the overall cost of ownership for the excavators.
This solution underscores the importance of utilizing advanced forging techniques and materials in heavy-duty applications like mining. SSP’s provision of high-quality forged mining teeth showcases their commitment to delivering innovative solutions that meet and exceed customer expectations. This successful outcome serves as a testament to the effectiveness of forging technology in optimizing performance and durability for specialized mining applications.
SSP Advantage:
SSP’s advantage lies in their technological expertise, ability to deliver high-quality forged products, extended lifespan compared to castings, customization capabilities, operational efficiency improvements, long-term cost savings, and commitment to customer satisfaction. These factors make SSP the preferred choice for customers seeking durable and optimized solutions for their mining equipment.
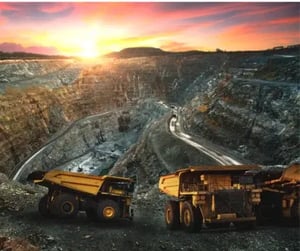
Forging Advantages
Railroad, mining, industrial machinery, and gear customers choose forgings over castings in critical application areas because they know quality can’t be compromised. Critical applications demand forging because it delivers:
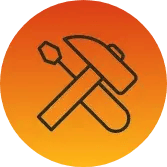
Stronger end products due to a tighter grain structure
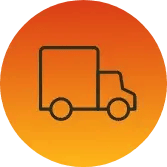
Products that are true to form with little porosity or cavities
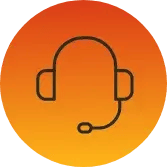
Fewer weak points because forging reduces the need to fabricate multiple components
Quality Assurance
Our quality management systems meet international standards, which means we consistently provide products and services that fulfill customer and regulatory requirements.

ISO 9001:2015 Certified
.webp?width=39&height=39&name=icon_1%20(1).webp)
AAR M-1003 Certified
American Association Railroads
.webp?width=39&height=39&name=icon_1%20(2).webp)
ISO 14000
Compliant
.webp?width=39&height=39&name=icon_1%20(3).webp)
Mitutoyo
FHM4CMM
.webp?width=39&height=39&name=icon_1%20(4).webp)
Magnetic Particle
testing certified
.webp?width=39&height=39&name=icon_1%20(5).webp)
Level three
PPAP capable