CASECASE STORY: Collaborative Innovation in Rail Car Component Development
- Home
- Case Stories
- Collaborative Innovation in Rail Car Component Development
Collaborative Innovation in Rail Car Component Development
Case Study: Collaborative Innovation in Rail Car Component Development
Customer: One of the largest Rail Car Manufacturers in North America
Industry: Rail Car Manufacturing
Challenge: Elevating Rail Car Component Design
In the intricate world of rail car manufacturing, precision and reliability are paramount. Our customer, one of the largest rail car manufacturers in North America, embarked on a mission to elevate their rail car component design. The challenge lay in developing a new style center plate that would allow automated welding into the sill greatly increasing production and quality to one of the most critical components of a railcar. With a dedication to pushing the boundaries of innovation, the customer aimed to enhance this component to meet stringent specifications that would optimize rail car performance.
Solution: Synergistic R&D Partnership
Recognizing the complexity of rail car component development, the customer sought a collaborative solution. Our internal Research and Development (R&D) team emerged as the ideal partner, poised to work alongside the customer’s engineers to craft components that transcended industry norms. By combining the customer’s domain insights with our R&D acumen, a strategic partnership was forged to steer the development process.
R&D-Driven Development: Fusion of Expertise
The heart of this collaboration resided in the fusion of our respective expertise. The customer’s engineering team and our R&D experts united to meticulously design and engineer the center plate. The journey was characterized by in-depth analyses, iterative adjustments, and exhaustive testing. Our teams worked in tandem to ensure the components adhered to the customer’s rigorous specifications while also meeting the demanding standards of rail car performance.
Results: Pioneering Innovation
The outcome of this R&D-driven partnership was nothing short of revolutionary. The concerted effort between the customer’s engineering team and our R&D experts culminated in the creation of a center plate that surpassed industry benchmarks. By embracing a collaborative ethos, the customer successfully translated their vision into tangible, high-quality components, thereby elevating the landscape of rail car manufacturing.
Advantage of Collaborative Innovation: Setting New Standards
This case study magnifies the immense power of collaborative innovation. The partnership between our customer’s engineers and our R&D team showcases the remarkable results that unfold when domain insights and advanced research converge. The ability to align R&D expertise with customer-driven specifications not only demonstrates our capabilities but also propels the customer to the forefront of the rail car manufacturing industry. This successful endeavor underscores our commitment to pioneering innovation and the transformative impact of working together to engineer solutions that redefine standards in the rail car sector.
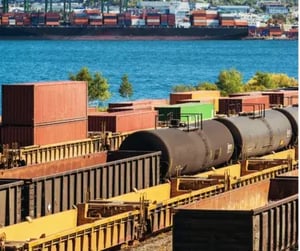
Forging Advantages
Railroad, mining, industrial machinery, and gear customers choose forgings over castings in critical application areas because they know quality can’t be compromised. Critical applications demand forging because it delivers:
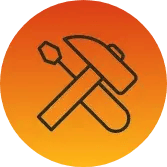
Stronger end products due to a tighter grain structure
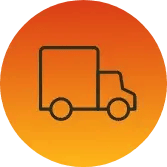
Products that are true to form with little porosity or cavities
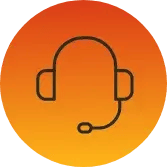
Fewer weak points because forging reduces the need to fabricate multiple components
Quality Assurance
Our quality management systems meet international standards, which means we consistently provide products and services that fulfill customer and regulatory requirements.

ISO 9001:2015 Certified
.webp?width=39&height=39&name=icon_1%20(1).webp)
AAR M-1003 Certified
American Association Railroads
.webp?width=39&height=39&name=icon_1%20(2).webp)
ISO 14000
Compliant
.webp?width=39&height=39&name=icon_1%20(3).webp)
Mitutoyo
FHM4CMM
.webp?width=39&height=39&name=icon_1%20(4).webp)
Magnetic Particle
testing certified
.webp?width=39&height=39&name=icon_1%20(5).webp)
Level three
PPAP capable